Cheese dairy Bräägg
For over 100 years, cheese has been produced on the Brääggfeld in Bazenheid. In 2009, the Manser family acquired the business. Before that, she had run a leasehold farm in Sedrun for nine years. As a master cheesemaker, Thomas Manser dedicates himself to milk processing and independent pig fattening. His wife, Bernadette, a trained baker and confectioner, runs the shop directly on the busy main street.
9602 Bazenheid
(Switzerland)
Farm
Electrical energy consumption
approx. 150'000 kWh/year
Cheese dairy of the future
The Bräägg cheese dairy focuses on energy efficiency and on producing and storing its own electricity. Cheese production is energy-intensive, and price increases for electricity and fossil fuels have a noticeable impact on production costs and margins.
The entrepreneurial spirit and energy of the family is palpable. Every year, it processes one million kilograms of milk into various semi-hard cheeses, soft cheeses, Mutschli and other specialities. Thomas Manser also keeps a thousand pigs in the fattening barn, which is directly adjacent to the cheese dairy. Breeding and fattening are carried out according to the IP-Suisse standard. The seal of quality, the red ladybird, distinguishes the meat from animal-friendly production. Mansers sell the cheese to wholesalers, and Micarna processes the beef. One-fifth of the production volume is marketed directly by the family.
Energy efficiency versus high prices
The production of dairy or meat products requires a lot of energy. The recent surge in the price of electricity and fossil fuels has also had a painful impact on many Swiss cheese dairies. Economic uncertainties and inflation also hurt consumers' desire to buy and purchase power. As a result, domestic cheese production shrank by 2.5 per cent in 2022, and the volume of Swiss cheese exported fell by 6.7 per cent. To remain competitive in the Swiss dairy business, you must focus on efficiency and energy costs.
Fromarte, the umbrella organization of Swiss cheese specialists, has a target agreement with the Energy Agency of the German Economy (EnAW) to increase energy efficiency and reduce CO2 emissions. The industry solution enables commercial companies to recover part of the CO2 tax. The prerequisite for this is reducing energy consumption by defined target values. Thomas Manser is also involved in this benchmark model, in which the participants' progress is compared with that of the most efficient cheese dairy within a group.
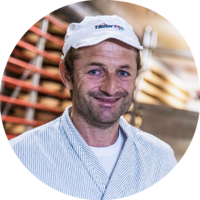
«IF THE FEEDING, MILKING OR COOLING TECHNOLOGY IN AGRICULTURE DOES NOT WORK DUE TO POWER OUTAGES, THIS IS CRITICAL. ESPECIALLY IN MILK PROCESSING, THE COLD CHAIN MUST BE ENSURED FOR QUALITY REASONS. FURTHER PROCESSING, ON THE OTHER HAND, REQUIRES A LOT OF HEAT. WITHOUT ALL THIS, THERE IS NO SWISS CHEESE.»
THOMAS MANSER, MASTER CHEESEMAKER & MANAGING DIRECTOR OF THE BRÄÄGG CHEESE DAIRY
Electricity production is higher than consumption
As a first step, the Mansers installed a small photovoltaic system with an output of 30 kilowatts, which was expanded by 10 kilowatts as part of an expansion of the barn. Two further expansion stages followed, each with 120 kilowatts and 80 kilowatts. Today, the total output of the plants amounts to a 240-kilowatt peak. Now, the enthusiasm and the urge to optimize have finally awakened: Manser and his team were actively involved in constructing the last plant.
Even before the plants were built, the fattening farm and the cheese dairy drew 150000 kilowatt hours of grid electricity per year. Manser has paid the highest monthly electricity bill, 3,000 Swiss francs. In the meantime, the income from the feed-in tariffs of his supplier, Regionalwerk Toggenburg AG (RWT), exceeds the costs of grid procurement in the high-yield months. And it cannot be ruled out that Manser will soon become a permanent net feeder.
Electricity storage for the security of supply
This is possible thanks to the electricity storage systems from eco coach AG from Brunnen (SZ). The battery storage specialist's systems make green electricity from its production available around the clock. This also applies during power outages: The system has an integrated emergency power, power reserve and island grid function. To ensure that the system works without being drawn from the public power grid, the family had to retrofit a grid disconnection device in front of their battery storage systems.
Depending on the configuration, the individual eco coach storage systems have capacities ranging from 26 to 65 kWh. The system can be expanded to up to six systems with 390 kWh. Four fully equipped storage systems are currently in use at Manser.
The battery storage systems are equipped with a fully-fledged energy management system by Brunner specialists. This system controls the energy flows between the producer and consumer sides based on measurement data for optimal energy efficiency, security of supply, and economic efficiency.
Self-consumption can be controlled
Optimization at the Bräägg cheese dairy is challenging, as cheese production follows fixed times, which makes performance peaks difficult to avoid. A new heat pump was installed by the Bräägg cheese dairy about a year ago. It is used for underfloor heating around 1,500 square metres in the two living areas and the hovel. After all, free-range pigs must be able to warm up in winter and cool down in summer. Manser's fattening farm also has its grinder for feed production, which allows him to respond to grain prices. The load profile of the grinder can be influenced in a similar way to cooling technology.

After the optimization is before the optimization
If you ask Manser about the next stage of expansion, it becomes clear that he will have fewer options in the future. "The problem is heat generation in winter," says Manser. Since neither a CHP plant nor biogas are options for him, he has his sights set on seasonal energy storage in the form of a sand storage tank. This is because the net-zero targets are considered to have been set.
These pose challenges for energy-intensive cheese production, especially in process heat. New ideas, solutions, and technologies are in demand. Thus, energy production and storage are likely to be included in the new industry guideline on energy efficiency in cheese dairies.
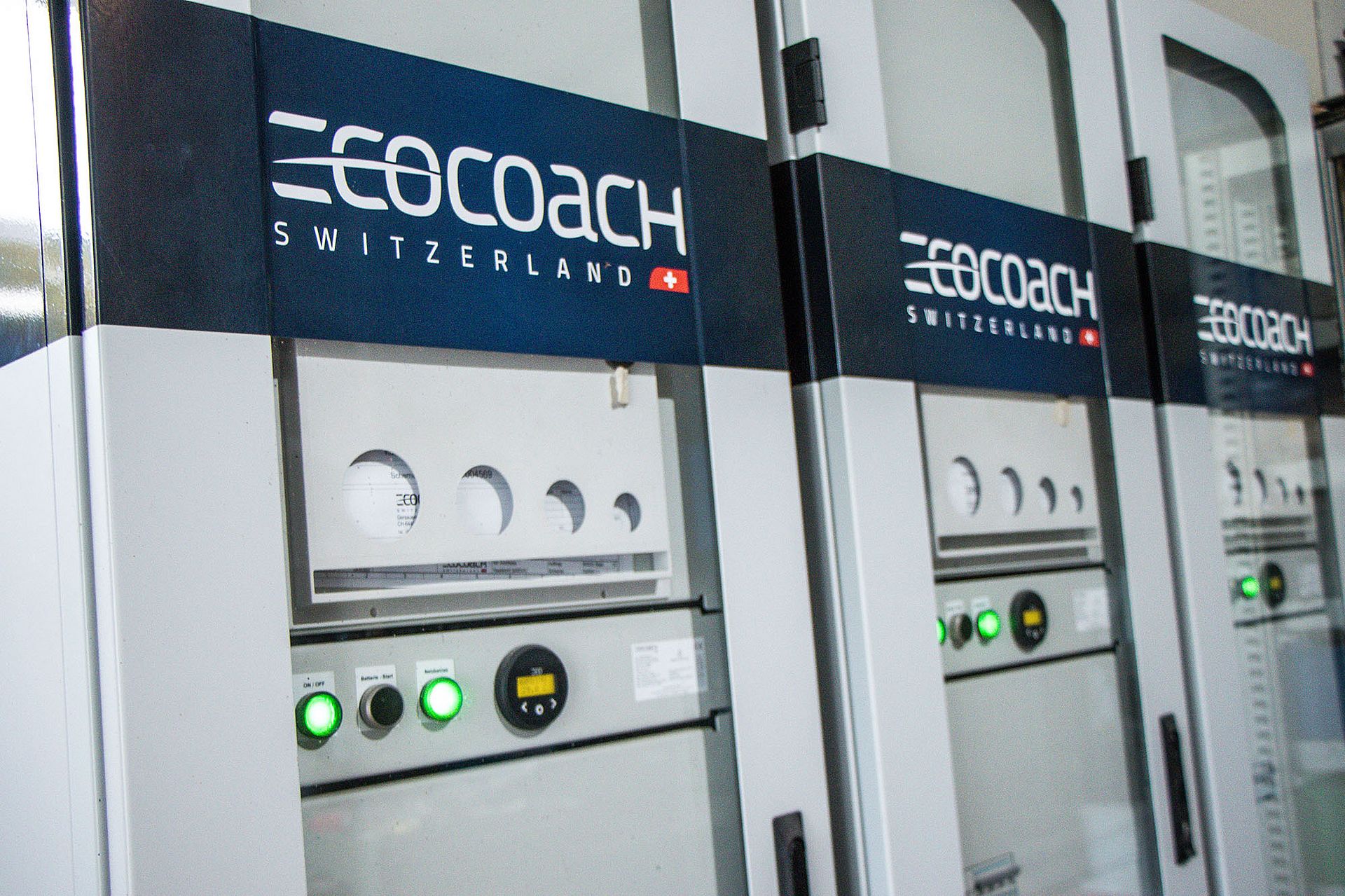
Are you interested in an on-site guided tour?
Then contact us today to arrange a viewing appointment with an ecocoach specialist.
Reference details
Photovoltaics |
|
---|---|
ecoBatterySystem | 4x batterie system
|
ecoEnergyCoach | Energymanagementsystem
|
ecoChargingCoach | No charging management / load management for charging stations |
ecoOneClick | No billing system for ancillary costs |
ecoSetupTool | Installer commissioning platform, allows configuration without programming knowledge |
ecocoach App | Advantages for farmers:
|
Smart Home | Not a smart home |
Particularities | Expansion of battery storage planned to increase self-consumption |
Participating companies |
|
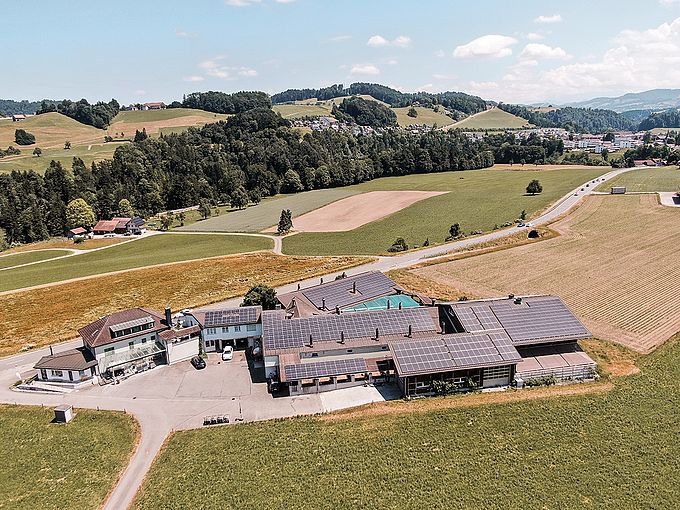
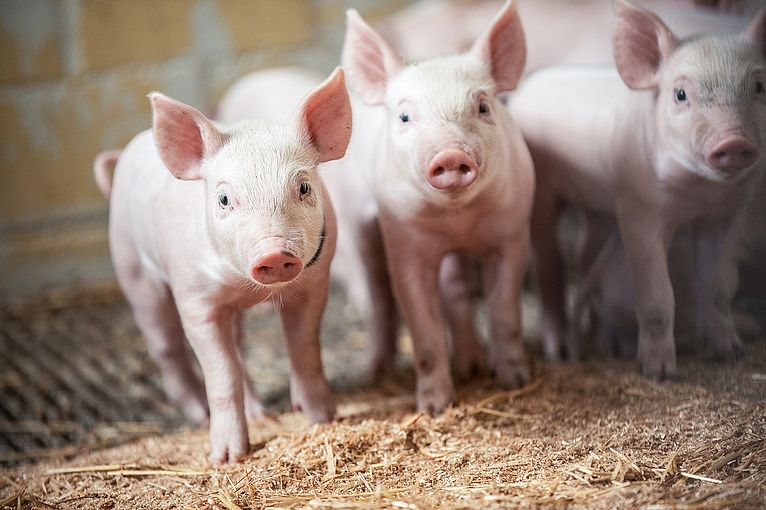
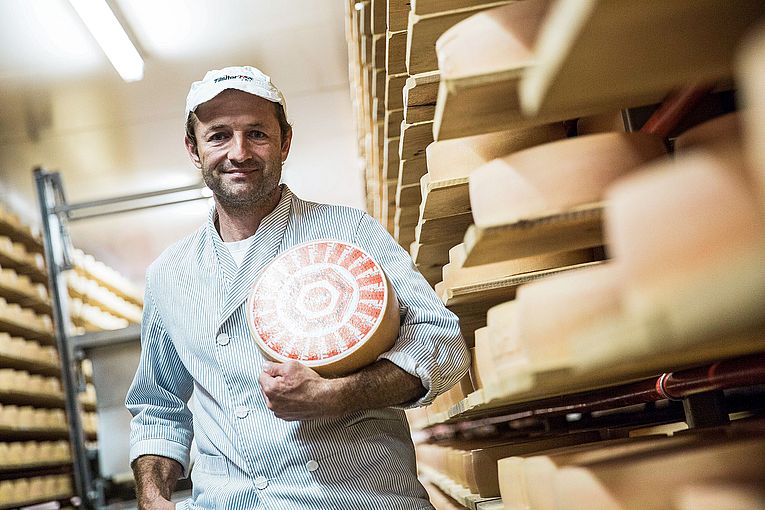

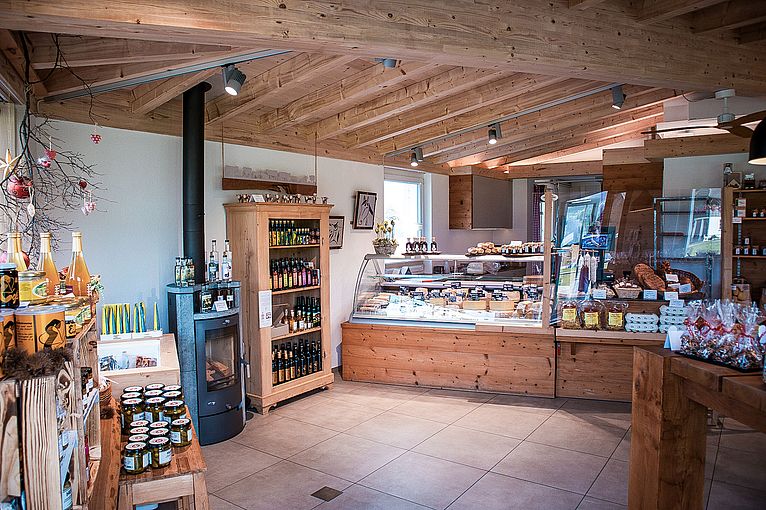
